A64 Bridge Foundation Strengthening
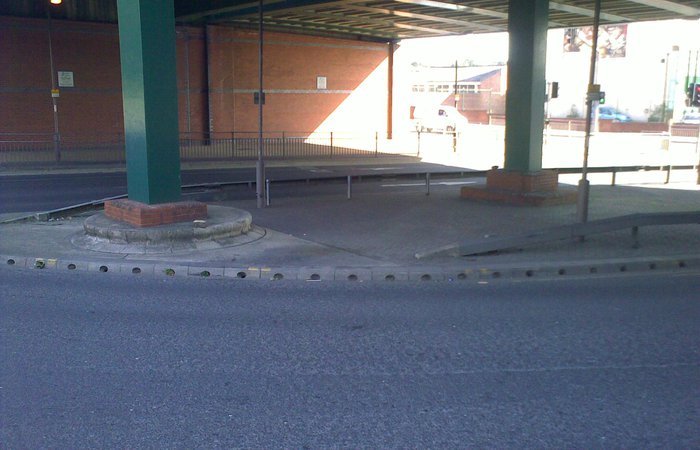
Byland Engineering has provided geotechnical consultancy support to Leeds City Council under a framework contract for some 10 years. One recent project involved the strengthening of foundations supporting steel box section columns to the bridge which carries the A64 New York Road, a principal route into the city, over Marshgate junction.
Following an assessment of the structure, damage to the columns due to vehicle collision was identified as an unacceptable risk. The solution in principle was to prevent catastrophic failure of the column by enhancing its fixity to the ground. The bridge columns are located within traffic islands and while existing kerbs and crash barriers provide limited impact protection, there is insufficient space to construct more robust protection around the columns without impairing the road layout and sight distances.
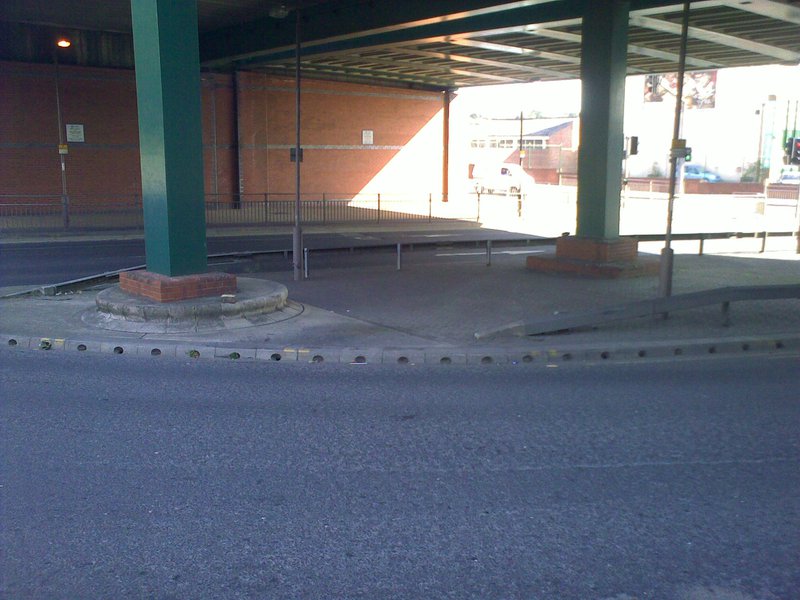
Bridge Support Columns
Byland provided the following services to the Council :
- Preparation of a geotechnical desk study
- Planning and documentation of an intrusive ground investigation
- Preparation of an Approval in Principal (AIP) document for the design
- Design of ground anchorages to BS EN 1997
- Preparation of anchor specification
- Visiting supervision of construction
- Assessment of installation records and stress test results
- Preparation of a validation report
Three bridge columns were selected for strengthening which comprised the installation of four number passive monobar drilled and cement grouted ground anchorages around each column and their connection to a new below ground reinforced concrete collar surrounding the column base plate.
The site investigation showed that some 2m of made ground, including concrete, overlies 2m of weathered bedrock and then an 8m thick bed of medium strong sandstone. Below this, mudstones with a thin coal seam were known to be present. It was concluded that the coal seam was unlikely to have been worked. The sandstone offered a suitable layer in which to fix the anchors. No buried services were anticipated.
For the 800kN service load, each anchor required a 47mm diameter Dywidag pre-stressing steel threadbar. A double corrosion protection system was chosen for the required 120 year service life. The anchor was designed with a free length of 4m and a bonded or fixed length of 6m.
After the traffic island pavement construction was removed, the anchors were installed in low headroom in 190mm diameter boreholes drilled using a tracked Beretta drill rig with rotary percussive drill system and air flushing. Prior to drilling, the concrete immediately below commencing surface was removed using diamond core drilling and a temporary plastic casing was used to support the remaining made ground and weathered (soil like) bedrock below.
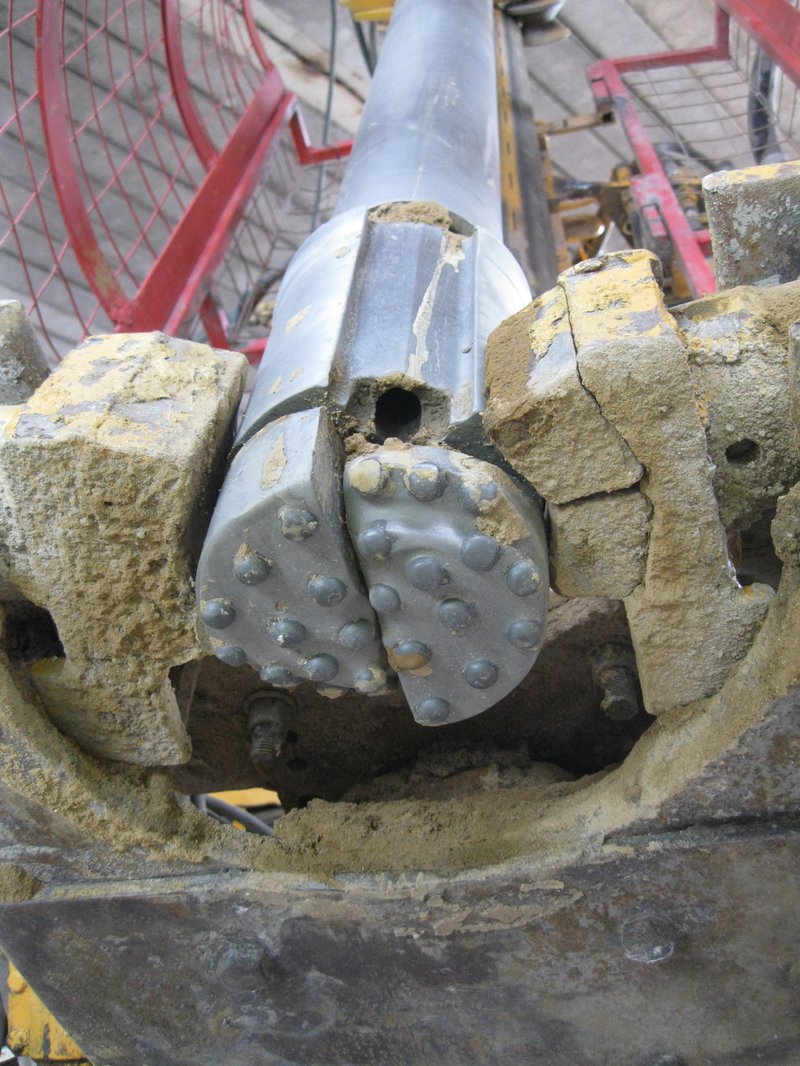
DTHH Drill Bit
During the construction of one ground anchor, a large grout take and a sudden fall in the drill rods indicated a subterranean void. Naturally, the initial concern was for the presence of mine-workings. Following re-examination of service records, contact with the local undertaker and the carrying out of aCCTV survey down the hole and in what turned out to be a fractured service pipe, it was concluded that the void was in fact an abandoned cast iron drain at 6m depth in the sandstone bedrock. As the fractured pipe had caused iron debris to be left in the hole, it was decided to vary the inclination of the anchor slightly to avoid the debris (which presented a risk of major damage to the drill string or drill rig) while still using the opening through the concrete at street level. In this way, the original anchor location, relative to the column, was sensibly achieved.
Each anchor was successfully installed and stress tested (as an acceptance test to BS EN 1537) to a proof load of 1000kN and then locked of to a nominal pre-load of 30kN. The load extension relationship and apparent free lengths were assessed by Byland Engineering to confirm that the anchors were performing as required.